How are polycarbonate mirrors made?
Polycarbonate mirrors are a popular choice in many applications due to their durability, versatility, and lightweight properties. They are used in a wide variety of industries, including automotive, construction, security, and even entertainment equipment such as racing goggles. But have you ever wondered how these mirrors are made? Let's take a closer look at the manufacturing process of polycarbonate mirrors.
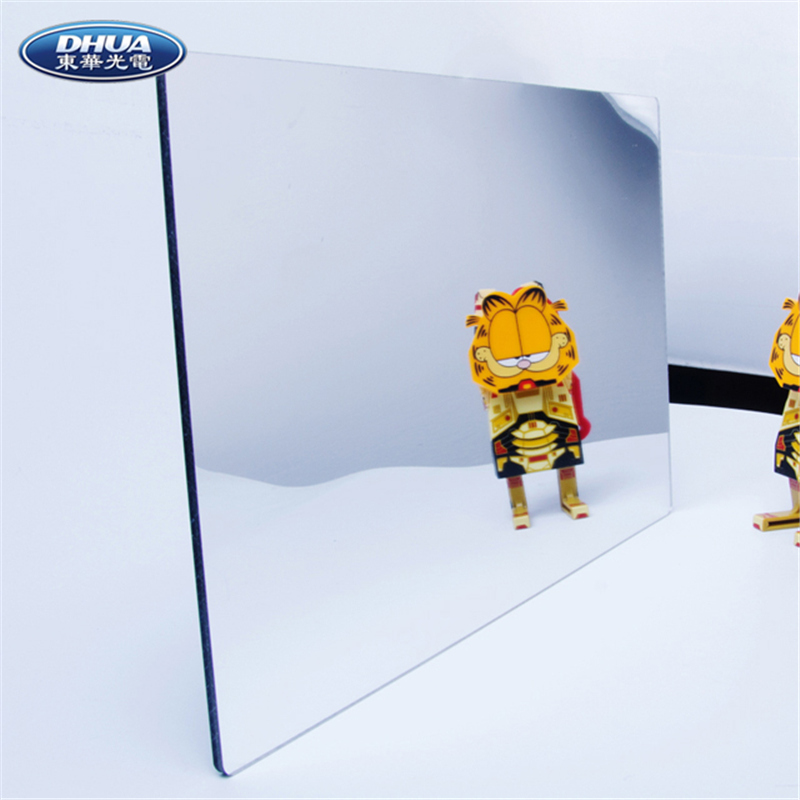
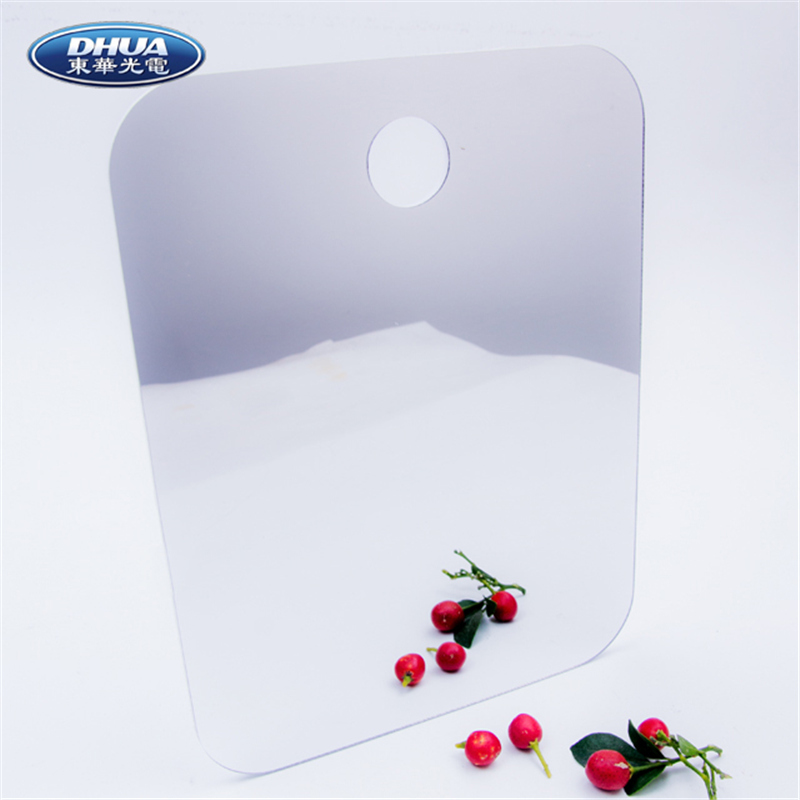
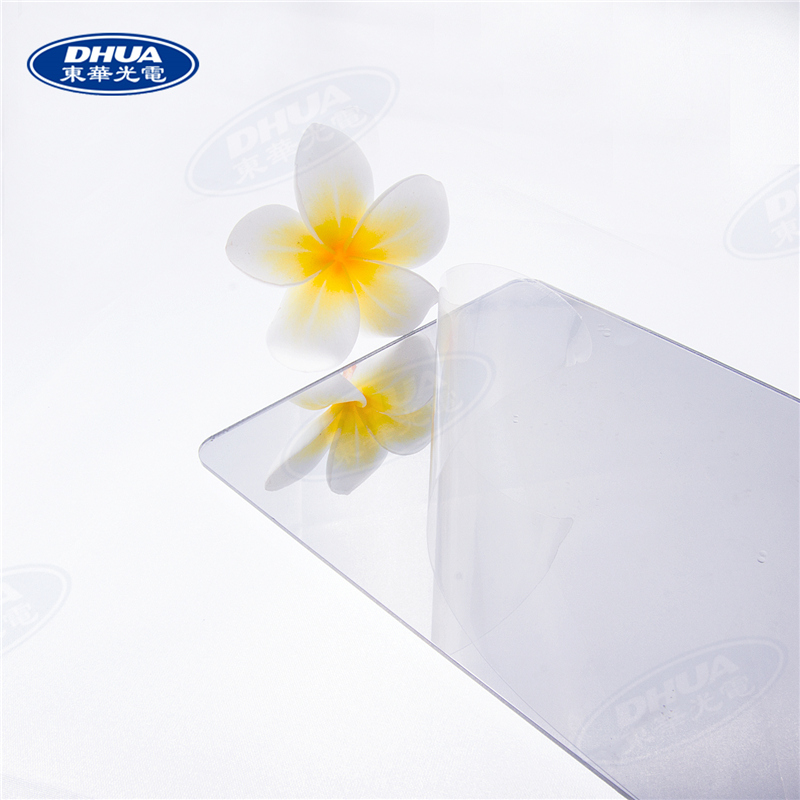
01 A polycarbonate mirror was originally a piece of polycarbonate, a thermoplastic polymer known for its exceptional strength and impact resistance. The manufacturing process begins with the extrusion of polycarbonate material. Polycarbonate resin is melted and extruded into flat, thin shapes to form polycarbonate lenses.
02 Additives are often mixed with polycarbonate resins during extrusion. These additives can enhance the transparency, UV resistance or impact resistance of mirror panels. The specific additives used may vary depending on the desired properties of the final product.
03 Additives are often mixed with polycarbonate resins during extrusion. These additives can enhance the transparency, UV resistance or impact resistance of mirror panels. The specific additives used may vary depending on the desired properties of the final product.
04 The next step in the manufacturing process is to apply a reflective coating to the polycarbonate panels. This coating gives the mirror its reflective properties. There are different methods for applying reflective coatings to polycarbonate sheets, including deposition processes or vacuum deposition processes.
05 During deposition, a thin layer of metal, such as aluminum, is applied to the surface of a polycarbonate sheet. This metallic coating reflects light, creating a mirror effect. During vacuum deposition, the metal coating is evaporated in a vacuum chamber and then condenses onto the surface of the sheet to form a reflective layer.
After the reflective coating is applied, the polycarbonate lenses are inspected again to ensure that the coating is even and free of any defects. The sheet is then cut to the desired size and shape.
Depending on its intended use, polycarbonate mirrors can be manufactured in different thicknesses. Thicker sheets are often used in applications requiring higher impact resistance, such as safety mirrors. Thinner sheets are typically used in applications where weight is a concern, such as automotive mirrors.
In addition to strength and impact resistance, polycarbonate mirrors offer other advantages over traditional glass mirrors. They are lightweight and easier to handle and install. They are also more resistant to shattering, which makes them a safer choice in environments where breakage is a concern.
Post time: Jul-12-2023